Industrial Fans
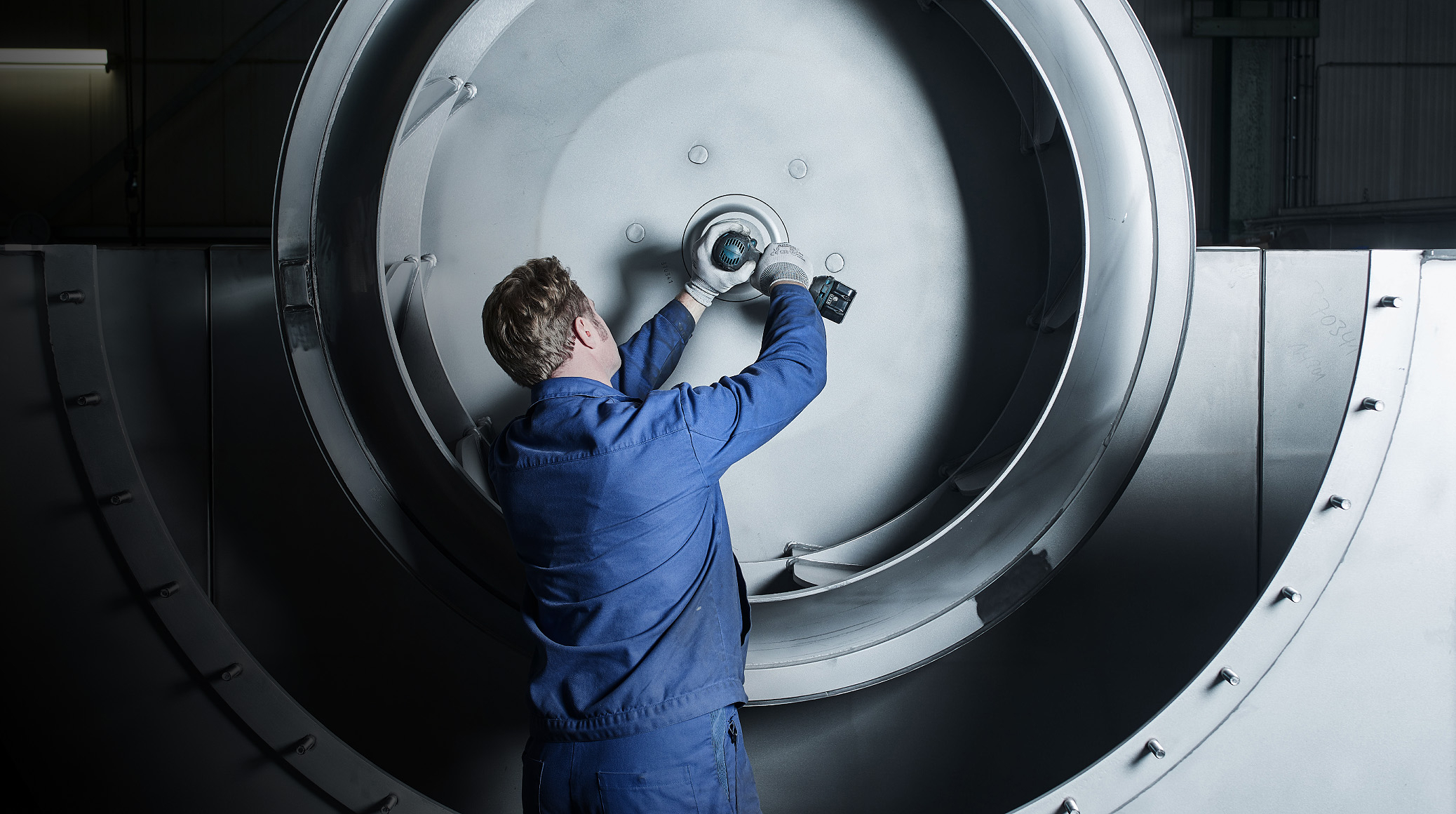
Our
series
As a leading manufacturer of industrial fans, we set standards for quality, performance and innovation.
Our broad product range includes a variety of construction types, design variants and equipment options. Each fan is individually designed according to your industry-specific requirements and equipped with all the options you need for reliable and perfect operation.
Plant operators from all over the world rely on Reitz due to the special depth of performance and diversity of variants. Exceptional solutions and engineering that masters challenges carefully and conscientiously are the prerequisites for smooth operation, even in critical areas of application. The technical design of our fans is based on DIN 24166, and we also meet the requirements of numerous international and industry-specific regulations and standards.
Equipped
for every
application
We offer a wide range of designs or design combinations for all our models to perfectly suit your area of application.
Pressure resistant
For systems with an inlet pressure of more than 0.5 bar
Pressure shock proof
Protected against pressure surges in the range from 0.2 to 10 bar
Gas-, Liquid- and Dustproof
For particularly challenging fluids such as toxic liquids or gases
Corrosion protection
Effective corrosion protection measures for hygiene and durability
Explosion protected
Explosion protection in accordance with the ATEX directive when conveying flammable dusts and gases
High temperature resistant
Suitable for extreme process temperatures up to 500 ºC and high outside temperatures
Wear protection
Special design and processing increases service life and avoids follow-up costs
Hygienic Design
Customized designs for hygienic operation
Even our basic program offers a wide range of centrifugal fans for the most diverse tasks and performance requirements. The modern production processes and the high level of vertical integration ensure high quality standards on the one hand and a very good price/performance ratio and optimum delivery times on the other.
For additional requirements, we develop and produce customized fans for all industrial applications. Our dedicated team will be happy to provide you with further information and technical advice. We look forward to working with you to find the optimum solution for your requirements.